Roman concrete, also called opus caementicium, was a material used in construction during the late Roman Republic and the entire history of the Roman Empire. Roman concrete was based on a hydraulic-setting cement. Recently, it has been found that it materially differs in several ways from modern Portland cement. It is widely acknowledged that Roman concrete is the most durable type of cement of its kind due to its incorporation of volcanic ash, which prevents cracks from spreading. By the middle of the first century, the material was frequently used, often brick-faced, although variations in aggregate allowed different arrangements of materials. Further innovative developments in the material, called the Concrete Revolution, allowed the construction of complex buildings such as the Pantheon: a temple which housed the world’s largest unreinforced concrete dome.
Roman concrete was typically faced with stone or brick, and interiors might be further decorated by stucco, fresco paintings, or thin slabs of colored marble. Made up of aggregate and cement, like modern concrete, it differed in that the aggregate pieces were typically far larger than in modern concrete, often amounting to rubble, and as a result, it was laid rather than poured. Some Roman concretes could be set underwater, which was useful for bridges and other waterside construction.
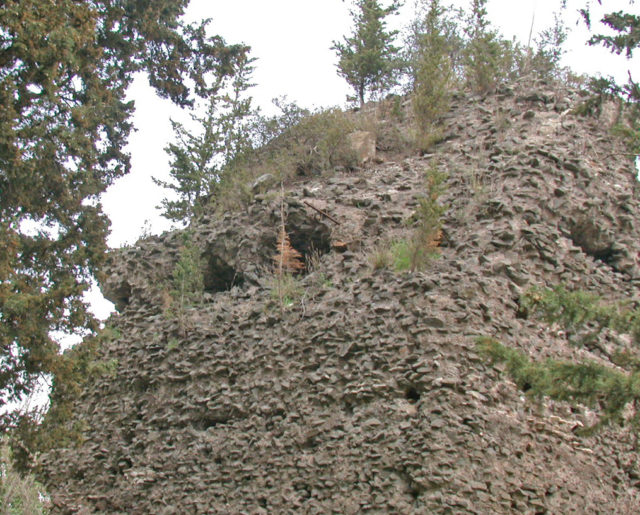
It is uncertain when the mixture was first developed, but it was clearly in widespread use from about 150 BC. However, some scholars believe it was invented around a century before that.
Vitruvius, writing around 25 BC in his Ten Books on Architecture, distinguished types of aggregate appropriate for the preparation of lime mortars. For structural mortars, he recommended pozzolana, which are volcanic sands from the sandlike beds of Pozzuoli brownish-yellow-gray in color near Naples and reddish-brown at Rome. Vitruvius specifies a ratio of 1 part lime to 3 parts pozzolana for cement used in buildings and a 1:2 ratio of lime to pulvis puteolanus for underwater work, virtually the same proportion mixed today for concrete used at sea.
By the middle of the first century, the principles of underwater construction in concrete were well known to Roman builders. The city of Caesarea was the earliest known example to have made use of underwater Roman concrete technology on such a large scale.
Rebuilding Rome after the fire in 64 AD, which destroyed large portions of the city, the new building code by Nero consisted of largely brick-faced concrete. This appears to have encouraged the development of the brick and concrete industries.
Gypsum and lime were used as binders. Volcanic dust, called pozzolana or “pit sand,” was favored where they could be obtained. Pozzolana makes the concrete more resistant to salt water than modern-day concrete. The pozzolanic mortar used had a high content of alumina and silica.
Concrete, and in particular, the hydraulic mortar responsible for its cohesion, was a type of structural ceramic whose utility was derived primarily from its rheological plasticity in the paste state. The setting and hardening of hydraulic cement derived from hydration of materials and the subsequent chemical and physical interaction of these hydration products. This differed from the setting of slaked lime mortars, the most common cement of the pre-Roman world. Once set, Roman concrete exhibited little plasticity, although it retained some resistance to tensile stress
The setting of pozzolanic cement has much in common with its modern counterpart, Portland cement. The high silica composition of Roman pozzolana cement is very close to that of modern cement to which blast furnace slag, fly ash, or silica fume has been added.
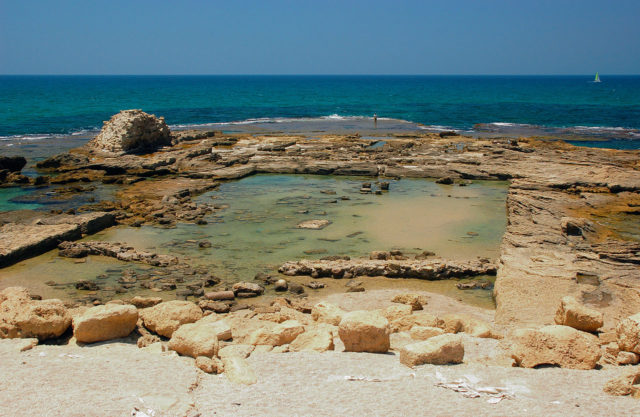
Compressive strengths for modern Portland cement are typically at the 50 MPa level and have improved almost ten-fold since 1860. There are no comparable mechanical data for ancient mortars, although some information about tensile strength may be inferred from the cracking of Roman concrete domes. These tensile strengths vary substantially from the water/cement ratio used in the initial mix. At present, there is no way of ascertaining what water/cement ratios the Romans used, nor are there extensive data for the effects of this ratio on the strengths of pozzolanic cement.
For an environment as prone to earthquakes as the Italian peninsula, interruptions and internal constructions within walls and domes created discontinuities in the concrete mass. Portions of the building could then shift slightly when there was a movement of the earth to accommodate such stresses, enhancing the overall strength of the structure. It was in this sense that bricks and concrete were flexible. It may have been precisely for this reason that, although many buildings sustained severe cracking from a variety of causes, they continue to stand to this day.
Another technology used to improve the strength and stability of concrete was its gradation in domes. One example included the Pantheon, where the aggregate of the upper dome region consisted of alternating layers of light tuff and pumice, giving the concrete a density of 1,350 kg/m3. The foundation of the structure used travertine as an aggregate, having a much higher density of 2,200 kg/m3.
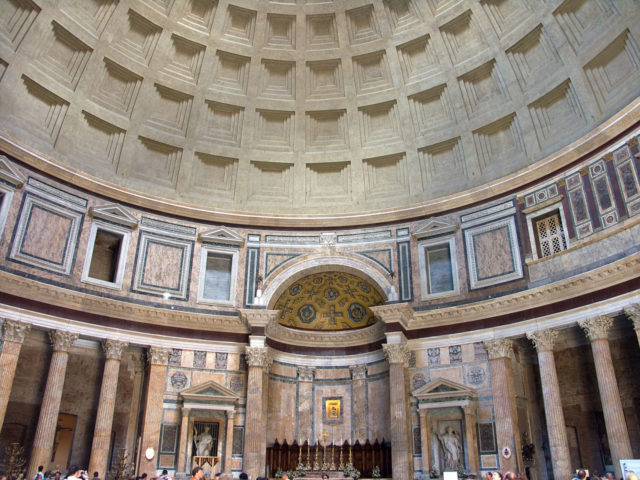
Recent scientific breakthroughs examining Roman concrete are gathering media and industry attention. Because of its unusual durability, longevity, and lessened environmental footprint, corporations and municipalities are starting to explore the use of Roman-style concrete in North America, substituting the volcanic ash with coal fly ash that has similar properties. Proponents claim that concrete made with fly ash can cost up to 60% less because it requires less aggregate, and that it has a smaller environmental footprint due to its lower cooking temperature and much longer lifespan. Usable examples of Roman concrete exposed to harsh marine environments have been found to be 2,000 years old with little or no wear